Achieving both safety and efficiency in pipeline extension projects is paramount, especially when dealing with critical resources like water, oil, and gas. It’s a balance of meticulous planning, advanced technology, and rigorous execution. Here’s how it’s done:
1. Meticulous Planning and Design
Safety and efficiency start long before any pipe hits the ground. This phase involves:
- Detailed Route Selection: Choosing optimal paths that minimize environmental impact, avoid densely populated areas, and navigate challenging terrain effectively. This often involves extensive geological surveys and geotechnical assessments.
- Advanced Engineering Design: Using sophisticated software to design pipeline networks that account for pressure, flow rates, material stresses, and environmental factors. This includes selecting the right pipe materials (e.g., high-grade steel, corrosion-resistant coatings) that can withstand operating conditions and external elements.
- Risk Assessment and Mitigation: Identifying potential hazards—from seismic activity to human error—and developing comprehensive plans to prevent or mitigate them. This includes emergency response protocols.
2. Cutting-Edge Technology and Equipment
Leveraging modern technology is crucial for both aspects:
- Automated Welding and Inspection: Employing automated welding robots ensures consistent, high-quality welds, significantly reducing human error. Non-destructive testing methods like ultrasonic or X-ray inspections verify weld integrity.
- Advanced Laying Techniques: Utilizing specialized equipment for trenching, pipe laying, and backfilling that can operate efficiently in diverse terrains, including automated pipe handlers and remotely operated vehicles (ROVs) for underwater installations.
- Geospatial Technologies (GIS and GPS): Using GIS for precise mapping of pipeline routes and infrastructure, and GPS for accurate positioning during installation. This helps avoid conflicts with existing underground utilities and ensures proper alignment.
3. Rigorous Quality Control and Testing
Ensuring the integrity of the pipeline is non-negotiable:
- Material Certification: All pipes and components must meet strict international standards for strength, durability, and corrosion resistance.
- Hydrostatic Testing: After installation, sections of the pipeline are filled with water and pressurized beyond their operational limits to detect any weaknesses or leaks before commissioning.
- Early Leak Detection Systems: Implementing real-time monitoring systems that can detect even small leaks or pressure drops instantly, allowing for rapid intervention. These can include fiber optic sensors, acoustic sensors, and pressure monitoring systems.
4. Skilled Workforce and Comprehensive Training
Human expertise remains at the core of successful and safe operations:
- Certified Professionals: Ensuring that all personnel involved, from engineers to welders and operators, are highly trained and certified in their respective fields.
- Safety Training: Regular and rigorous safety training programs covering all aspects of pipeline construction and maintenance, including emergency procedures, hazardous materials handling, and equipment operation.
- Environmental Awareness: Training teams on best practices for environmental protection to minimize disruption to ecosystems during construction and operation.
5. Continuous Monitoring and Maintenance
Safety and efficiency are ongoing commitments:
Preventive Maintenance Programs: Establishing proactive maintenance schedules for all pipeline components, pumping stations, and associated infrastructure to prevent failures.
Integrated SCADA Systems: Implementing Supervisory Control and Data Acquisition (SCADA) systems for centralized monitoring and control of pipeline operations, allowing for real-time adjustments and anomaly detection.
Regular Inspections: Conducting routine aerial, ground, and in-pipe (using “smart pigs”) inspections to identify potential issues like corrosion, cracks, or external damage before they become critical.
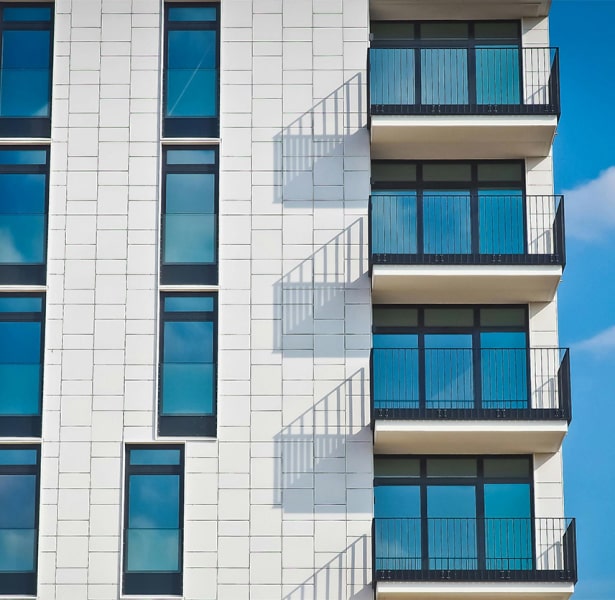
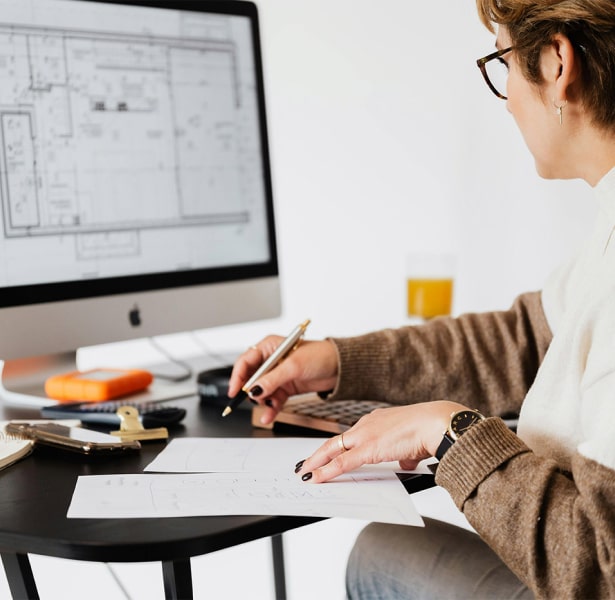